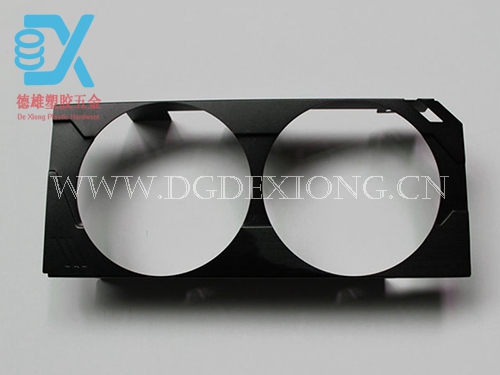
Product introduction
Sheet metal material | Hot rolled plate | Sheet metal thickness | 10-50(mm) | Processing size / length * width * height | 200*250(mm) |
Chassis | Chassis | Blanking method | Shearing machine | tolerance | 25-100 |
Processing procedure | Flanging, embedded flanging, bending, rib, stamping, punching, grooving, cutting, fillet, forming, unfolding | surface treatment | Electroplating colorful zinc | Proofing cycle | 4-7day |
Processing steps of parts processed in sheet metal workshop
Product preliminary test, product processing and trial production and batch production. In the process of product processing and trial production, timely communicate with customers and obtain the evaluation of corresponding processing before mass production
Laser drilling technology is the earliest practical laser technology in laser material processing technology. In the sheet metal workshop, pulse laser is generally used for laser drilling, which has high energy density and short time, and can be processed for 1 μ M is especially suitable for processing small holes with a certain angle and thin materials. It is also suitable for processing deep small holes and micro holes on parts with high strength and hardness or brittle and soft materials. Laser can realize the drilling processing of burner parts of gas turbine, and the drilling effect can realize three-dimensional direction, and the number can reach thousands. Materials that can be perforated include stainless steel, nickel chromium iron alloy and Hastelloy based alloy. Laser drilling technology is not affected by the mechanical properties of materials, and it is easy to realize automation. With the development of laser drilling technology, the laser cutting machine has realized automatic operation. The application in the sheet metal industry has changed the processing method of traditional sheet metal technology, realized unmanned operation, greatly improved the production efficiency, realized the full-automatic operation in the whole process, driven the development of sheet metal economy, improved a level in the drilling effect, and the processing effect is remarkable.
Common materials
1. Galvanized steel sheet SECC
The substrate of SECC is a general cold-rolled steel coil, which becomes an electro galvanized product after degreasing, pickling, electroplating and various post-treatment processes in the continuous electro galvanized production line. SECC not only has the mechanical properties and similar processability of general cold-rolled steel sheets, but also has superior corrosion resistance and decorative appearance. It has great competitiveness and substitutability in the market of electronic products, household appliances and furniture. For example, SECC is widely used in computer chassis
2. Ordinary cold rolled sheet SPCC
SPCC refers to the continuous rolling of steel ingot into steel coil or sheet with required thickness by cold rolling mill. There is no protection on the surface of SPCC, which is easy to be oxidized when exposed to the air. Especially in humid environment, the oxidation speed is accelerated and dark red rust appears. The surface shall be painted, electroplated or otherwise protected during use
3. Hot dip galvanized steel plate SGCC
Hot dip galvanized steel coil refers to the semi-finished products after hot-rolled pickling or cold rolling, which are cleaned and annealed, immersed in the zinc melting tank with a temperature of about 460 ° C, and then coated with zinc layer, and then quenched, tempered, leveled and chemically treated. SGCC material is harder than SECC material, with poor ductility (avoiding deep pumping design), thicker zinc layer and poor weldability
4. Stainless steel SUS304
One of the most widely used stainless steels, because it contains Ni (nickel), it is richer in corrosion resistance and heat resistance than the steel containing Cr (chromium). It has very good mechanical properties, no heat treatment hardening phenomenon and no elasticity
5. Stainless steel SUS301
The content of Cr (chromium) is lower than that of SUS304 and the corrosion resistance is poor. However, after cold processing, it can obtain good tension and hardness in stamping processing, and has good elasticity. It is mostly used for shrapnel spring and anti EMI.